АМО Ф-15 бортовой автомобиль
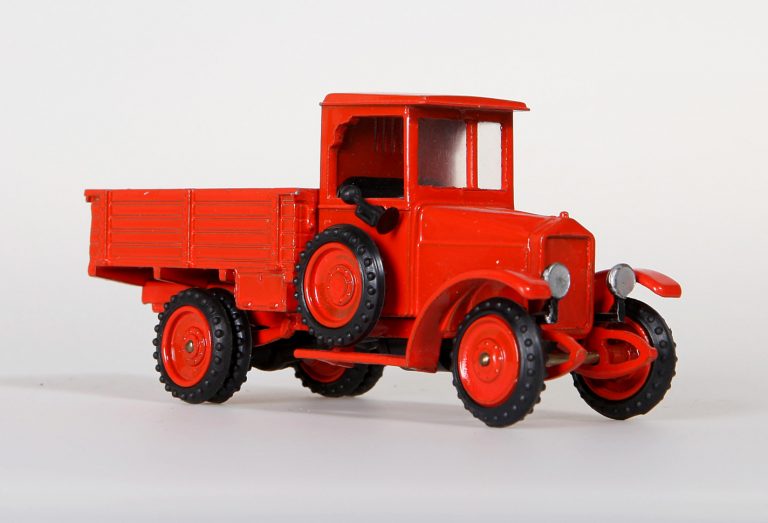
АМО Ф-15 4х2 бортовой автомобиль грузоподъемностью 1,5 тонн, модель 2-ой серии, руль справа, мест: 2, вес: снаряженный 1.92 тонн, полный до 3.4 тонн, максимальная скорость 42.5 км/час.
Двигатель: 35 лс
всех АМО Ф-15 в пределах 6500 экземпляров, АМО г. Москва, 1924/26-31 год выпуска.
Описание оригинала
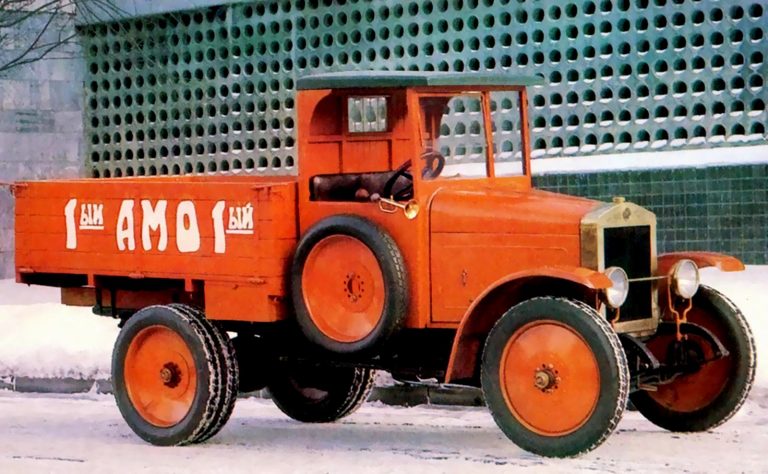
Начало выпуска:
Окончание выпуска:
Файлы
Из книги Канунникова С.В. и Шелепенкова М.А. под редакцией Маркова Н.С. «Отечественные грузовые автомобили». - Орел, ООО «САЛОН, 2018.
АМО Ф-15 представлял собой серьезно переработанный итальянский грузовик FIAT 15 ter образца 1915 г., на который завод имел всю техническую документацию. Первый АМО, полностью из отечественных деталей, собрали в ночь на 1 ноября 1924 г., а 7 ноября 1924 г. машины из первой партии, выкрашенные в красный цвет, приняли участие в пролетарской демонстрации на Красной площади в Москве.
Главным конструктором машины был В.И. Ципулин. Его ближайшие помощники: Е.И. Важинский (готовил рабочие чертежи), Б.Д. Страканов (пересматривал конструкцию деталей FIAT), И.Ф. Герман (кузовные работы), Н.С. Королев (сборка). Подготовкой производства занимались также тогдашний директор завода Г.Н. Королев, технический директор С.О. Макаровский, главный инженер В.Г. Соколов.
В 1927 г. машины получили кабину с жесткой, а не брезентовой крышей. С этого же времени некоторые АМОФ-15 имели аккумулятор, электрическое освещение, стартер и звуковой сигнал. В 1929 г. предприняли попытку модернизации АМО Ф-15 с повышением грузоподъемности до 2 т за счет нового заднего моста. Опытный образец, иногда называемый АМО Ф-20, изготовили в 1930 г., но надобность в нем уже отпала, так как для завода был подобран новый импортный грузовик.
АМО Ф-15 отличала хорошая проходимость, но низкая надежность, в том числе и из-за несовершенства технологии производства.
Модификации:
АМО Ф-15 - автобус (1925-30 г.);
АМОФ-15- санитарный (1925-30 г.);
АМО Ф-15 - пожарный (1926-30 г.);
АМО Ф-15 - радиофургон (1926-29 г.);
АМО Ф-15 - штабной с открытым пассажирским кузовом (1926-29 г.);
АМО Ф-15 - тюремный фургон (1926-27 г.);
АМО Ф-15- специальный фургон (192 7г.);
АМО Ф- 15СП - специальное шасси под бронеавтомобиль с двумя постами управления (1927-31 г.,
бронеавтомобили изготавливал Ижорский завод);
АМО Ф-15 - почтовый автобус (1928 г.).
Из брошюры «Завод АМО» , автор Ф. Святенко, Госиздат 1929 г.
Завод заработал.
С 1921 года на заводе начинают подумывать о том, чтобы ввести плановость в работе и выпуск однотипных машин, используя опыт автомобильного производства в Америке и Европе. С этой целью создается конструкторское бюро, приступившее к разработке имеющегося патента полуторатонного грузовика «Фиат» применительно к русским условиям.
Нужно было еще приобрести станки, инструменты. Ощущался острый недостаток в приспособлениях и материалах, приходилось применяться к имеющимся и конструировать новые.
В 1923 г. за 9 месяцев было выпущено из производства восстановленных машин «Уайта» 86 штук, и подготовлялись чертежи и приспособления для типа «Фиат».
Только в 1924 году завод по настоящему оживает. За этот год на заводе «АМО» было отремонтировано 25 автобусов «Уайта», которые были использованы в Крыму и на Кавказе. Было решено выпустить к годовщине Октябрьской революции новые грузовики в 1.5 тонны типа «Фиат». Десять штук новеньких машин к Октябрьским дням были сделаны. Эти красные пионеры «АМО» принимали участие в демонстрации на Красной площади.
Перед этим последние два месяца работали сверхурочно. Накануне демонстрации работа неустанно кипела пять ночей. Были рабочие, которые работали без сна по 48 часов подряд. Наконец установлены последние детали, купленные за границей «Магнето». Маляры закончили окраску кузовов. Новенькие машины, переполненные амовцами, гордо двигались в рядах московского пролетариата!
Чтобы показать достигнутые успехи на фронте автостроения, был организован первый автопробег трех машин от Ленинграда до Москвы и обратно через Лугу — Псков Смоленск. Пройдено было 2000 километров в 62 часа 29 минут, при полной 1.5-тонной нагрузке, средней скоростью в 32,2 километра в час, без малейшей поломки. Комиссия пробега признала годность машин, и заводу был присужден приз, а от ЦИКа была объявлена благодарность. Этим рабочие «АМО» открыли новую страницу в истории русского автомашиностроения.
Дорога откоыта.
Производство постепенно разрастается, выпуск в 1924/25 г. значительно увеличился; в этом году было выпущено 100 новых машин. В 1925/26 г. завод «АМО» сделал 275 машин, из них 6 автобусов собственной конструкции, 6 пожарных линеек, оборудованных на заводе.
Налицо успехи и в области снижения себестоимости машины. За 1924/25 г. первый выпуск стоил по 18 000 руб. за штуку, второй - 13 000, третий - 11000. В 1925/26 г. первая партия стоила по 9727 р. 99 коп. за штуку, вторая - 8360 р. 16 коп., автобусы по 18 909 р. 92 коп., пожарные линейки по 15106 р. 93 коп.
В том же 1925 году завод «АМО» выступает на арену состязания всесоюзного автопробега наравне с машинами старых заграничных фирм Круппа, Бенца, Мерседеса, Фиата, Форда и других. Завод «АМО» выставил две своих машины №№ 106 и 107. Нежные, заграничные автомобили, созданные для хороших дорог, не выдержали испытания в наших условиях, и грузовики «АМО», руководимые опытными водителями, прибыли первыми в Москву.
Еще лучше это было доказано (в 1925) пробегом машин «АМО» с целью изыскания дорог: Москва—Тифлис через Тулу—Орел—Курск—Харьков по шоссе, а дальше по грунтовой дороге через Ростов — Армавир — Пятигорск — Владикавказ и по Военно-грузинской дороге в Тифлис.
Пройдено было в этом пробеге всего 2155 километров.
К десятой годовщине власти советов завод «АМО» достиг еще больших успехов. По выработанному плану завод за 1927 год должен был выпустить 420 штук шасси на сумму в 6601 503 рубля, а выпустил 425 штук. Наши шасси сделаны с таким расчетом, что на них могут быть помещены кузова разных типов: автобусы, скорей помощи, пожарные линейки и пассажирские легковые. Пока легковых машин у нас сделано 5, пожарных —12, скорой помощи—10, автобусов— 50. С выпуском мы имеем такое положение: в 1924/25 году сделано 100 шасси, в 1925/26 - 275, в 1926/27 в 425, в 1927/28 - 609.
В 1924 г. рабочих было 1 213 человек, служащих—224 чел., в 1926/27 г. рабочих—1 495 человек и служащих—334 чел., а в настоящем 1928 году всего 2300 рабочих и служащих.
Как у нас делают автомобиль.
Начнем наш краткий обзор с заготовительных цехов—кузнечного и литейного. В кузнечном кипит работа. Вот воздушный молот, работающий сжатым воздухом, кует при посредстве особых штампов шатуны. Другой такой же молот кует диски для разных шестерен. Дальше протягиваются заготовки для коленчатых валов, а там из огромной, весом в 400 килограмм, болванки куют задний мост для трехтонных грузовиков. Печи выбрасывают раскаленные бесформенные куски стали, из которых после нескольких ударов молота получаются детали от рукоятки до оси автомобиля. Детали эти потом окончательно обрабатываются в других цехах. В воздухе стоит звон ударов молотов по наковальням.
Дальше, в прессовом отделении стоят гиганты-прессы рядом с печами. Вот рабочие вытащили длинную полосу стали и положили на штамп под пресс. Пуансон штампа опустился на полосу, сжал ее вовнутрь штампа. Захрустел металл, застонал пресс. Поднялся пуансон, и глядишь из плоской стали образовалась рама для шасси автомобиля.
Тут же лежат стальные листы, вырезанные крестообразно. С ними будет поступлено так же, как и с рамой, только выйдет из них уже картер (коробка) заднего моста автомобиля. В рессорном отделении, вручную, делают рессоры. Рабочий выгибает стальные полосы, укладывает их лист к листу так, чтобы и просвета не было между ними. Потом нагревают эти листы в печи докрасна, калят в масле и после сборки пробуют на прогиб под давлением электропресса.
Идем в конец двора, в литейный цех. Около него груды старого лома чугуна и ярусы военных снарядов. Зачем это? Все это пойдет на плавку стального и чугунного литья. Стальное литье плавят в электроплавильной печи английского происхождения фирмы «Электрометалл», работающей по типу «Эру». Эта печь дает за один раз до 2 тонн, стального литья. Электрическую энергию шлет Каширская станция. Зарядят печь разным стальным ломом, а через несколько часов готов жидкий металл. Под горловину печи подъемным краном подставляют большой ковш, подвешенный к крану. Он медленно движется по воздуху. Вот он остановился над первой опокой (формой для литья). Рабочий нажимает рычаг клапана ковша, и льется огненная сталь. Так идет процесс заливки, а через некоторое время опоки раскрываются, и появляется дымящаяся деталь машины.
Вот и вагранка «Мечта». Вагранка расплавляет чугун для отливки деталей. Такая деталь, как блок-цилиндры, требует сложной формовки; в ней целый лабиринт ходов, переходов, простенков, отверстий для цилиндров. Над тем, чтобы по модели сделать форму для отлива, работают опытные литейщики. Сам мастер следит за ходом работы и составом чугуна.
Дальше натыкаешься на две горки. От них пышет жаром, рабочие открывают люк и извлекают в тигле расплавленную медь и бронзу для отлива бронзовых деталей (подшипников, насосов и т. п.). В самом углу стоят два барабана, это ретортные нефтяные печи для плавки алюминия.
По отливке детали отправляются в обрубное отделение. Здесь—резкий грохот... Это в большом особом барабане, вращающемся с бешеной скоростью, очищаются от земли и грязи крупные и мелкие детали. Такие крупные детали, как блок-цилиндры, и др., которые в барабан заложить нельзя, обрубаются и очищаются пескоструйным аппаратом.
В обрубном отделении происходит также проверка всего литья. После этого все детали направляются в механический цех. Здесь сердце завода! В уши врывается разноголосая песня станков. Всякий станок делает свое особое дело. Расположены они по группам: здесь токарные, там строгальные, дальше - фрезерные, шлифовальные, а особняком стоят автоматы. Автомат не требует, чтобы около него стоял рабочий; один человек обслуживает четыре автомата. Вот, например, автомат «Глиссонон». Он ходуном ходит во все стороны—вниз, вверх, влево, вправо и продольно. Он обстрагивает зубья на круглом диске шестерни. А вот особый шлифовальный автомат, заменяющий 4 старых станка. Деталь на нем продвигается, вращаясь меж двумя камнями, и шлифуется. Все эти автоматы американские и дорогостоящие.
В цеху сверлильных станков вы обращаете внимание на роторный кондуктор-приспособление с точно расположенными, запрессованными стальными втулками для направления сверл, позволяющее быстро и точно сверлить отверстия в изделиях со всех сторон, вращая кондуктор вместе с изделием в специальной станине. На другом станке подобное же приспособление для другой детали. Таких приспособлений есть немного, есть и такие, которые придуманы самими рабочими. В механическом цеху окончательно отрабатываются все детали для автомобиля.
Прежде чем войти и выйти из механического цеха, деталь предварительно побывает в термическом отделе, где ее или смягчают—отжигают после кузницы, или делают более твердою,—закаливают до и после обработки в механическом цеху.
Побывав на окончательной отделке, деталь уходит в сборочное отделение. Здесь все детали собираются в шасси; получается нижняя часть автомобиля без кузова. Подвозят моторы; подъемным краном устанавливается мотор на предназначенное ему место на раме шасси, за ним устанавливают коробку скоростей, а дальше устанавливают задний мост, подвешивают рессоры, ставят оси. Звенит ключ, шуршит пила слесаря, стучит молоток, и видишь, как на твоих глазах растет машина; ставят радиатор, подводят колеса, вынуты козелки, на которых стояла рама шасси, стала машина на свои ноги-колеса.
Завертел человек ручкой, запыхтела, зашумела машина, тронулась с места. И пошла машина в кузовной отдел надевать на себя костюм—кузов да прикраситься в путь-дорогу. За ней следует другая, и так идет плановая работа в этом цеху. Надо отметить, что окончательная сборка шасси производится всего двумя бригадами. В них 14 человек. Конечно сначала собираются группы, т. е. отдельно мотор, коробка скоростей, задний мост, передняя ось, рулевое управление. Здесь над ними работают 70—80 пар рук и только после регулировки поступают на окончательную сборку.
Кузовной отдел это уже совсем другая отрасль труда, здесь делают из дерева те самые кузова, что мы видим на каждом автомобиле. Тут в сушилах сушат дерево, там высушенное дерево режут и строгают на станках. А на втором этаже собирают, склеивают доска к доске, шип к шипу, и выходит кузов. Едет он вниз на подъемной машине. Там его жестяники одевают в жестяные покровы. А уж тут маляры стоят с кистями, да с красками. Стекольщики ему окна вставят, обойщики сидения пристроят. А в сторонке уже и шофер стоит, ожидает, когда все готово будет. На пробу, километров сто отмахают, и если нет порчи, значит, машина готова.
В кузовном отделе изготовляются кузова не только для разных типов машин завода «АМО», как то обыкновенные грузовики, пожарные линейки, машины скорой помощи, легковые и другие, но и для автомобилей «Нами» и заграничных «Лейланд, «Зауэр». Постройка кузовов идет удачно, благодаря опытности мастеров, умелому руководству и специально созданному конструкторскому бюро.
При этом отделе имеется обойная мастерская, где заготовляются кожаные сидения, брезентовые верха для кузовов и производятся все обивные работы. Малярный отдел заготовляет разные краски для окраски автомобилей, он же имеет свою никелировочно-гальваническую мастерскую, где бронзируются и никелируются железные и медные части шасси и кузова.
В модельной мастерской кузовного отдела строят из дерева и из металла модели в литейный цех для отливки деталей машины. Есть также слесарно-механическая мастерская и прессовое отделение, где заготовляются все необходимые принадлежности кузовного дела. Тут же находится и медницкая и жестяная мастерские, где строят радиаторы, обшивку кузовов. Здесь вместо склепки листов употребляют электросварку.
Скажем несколько слов о таком важном подсобном цехе, как инструментальный. В нем делается инструмент и различные приспособления для всего завода. Тут требуется особо тщательная и кропотливая работа слесарей-инструменталыциков, умеющих работать на всех станках. Делаются лекалы, микрометры, калибры, сверла, метчики, плашки—словом, весь необходимый инструмент заводу. Точно так же важна, ответственна и точна работа в отделе, где изготовляются штампы. Тут не только надо очень хорошо уметь работать на станке, но и от руки с зубилом да пилой зависит очень многое. Должна быть максимальная точность и соответствие чертежам. Эти два отдела дают возможность заводу рационализировать свое производство все больше и дальше.
Есть при заводе и металлургическая лаборатория. Оборудованная новейшими испытательными станками и аппаратами, она проверяет качество поступающего на завод металла. Металл здесь пробуется на разрыв, на сжатие, и благодаря такому испытанию предупреждается брак автомашины. Химическая лаборатория анализирует состав литья, а также предупреждает брак.
За годы оформления и укрепления завода, вокруг него вырос целый лес общественно-производственных организаций. Клуб, большая библиотека, ясли живут полноправным темпом. А амовские спортивные команды давно известны как победители во многих союзных состязаниях.
Заключение.
Наш завод сделал уже 1000 машин. Все нужное для производства мы изготовляем сами, за исключением магнето, ободов, которые ввозятся из-за границы. Автомобильное производство на «АМО» входит в прочную колею, работа развивается без перебоя. По двору завода все чаще и больше пробегают новенькие, машины. Бегают они и в Москве, и в Туле, и на Ленских приисках, на Кавказе, в Крыму, Азербайджане, Семиречьи. Дальнейшая перспектива завода—взяться за более крупную машину.